Silica was identified as a workplace hazard identified by the Occupational Safety and Health Administration (OSHA). OSHA created guidelines to protect workers, especially in the construction industries, from exposure to respirable crystalline silica.
What is Respirable Crystalline Silica
Silica is the basic component of sand and rock. It’s in construction materials such as:
- Concrete, concrete block, cement, and mortar
- Masonry, tiles, brick, and refractory brick
- Granite, sand, fill dirt, and topsoil
- Asphalt-containing rock or stone
- Abrasive used for blasting
- Chipping, sawing, grinding, hammering, or drilling
- Crushing, loading, hauling, or dumping
- Building demolition
- Power cutting or dressing stone
- Facade renovation, including tuck-point work
- Abrasive or hydro blasting
- Dry sweeping or pressurized air blowing
- Tunneling, excavating, or earth moving
What are the risks when exposed to crystalline silica?
When very small (respirable) silica dust particles are inhaled they can penetrate deep into the lungs causing a disease called silicosis. Silicosis is a disabling, irreversible, and sometimes fatal lung disease for which there is no cure. Since silicosis affects lung function, it makes you susceptible to lung infections such as tuberculosis. For smokers, this is more hazardous, as smoking damages the lungs and adds to the damage caused by breathing silica dust. The other bad news is that crystalline silica is also a known carcinogen which means it can cause lung cancer.
What do you do to minimize Silica exposure risks?
- Engineering Controls
- Respirators and Protective Equipment
- Training
However, even with appropriate measures to control silica, some workers may still be affected. For this reason, periodic medical examinations are important for determining if the control measures in place are effective and if workers are suffering from any of the effects of silica exposure. This is known as medical surveillance and can be considered to be a method of early detection and prevention of silicosis.
Engineering Controls
Engineering controls are methods of designing or modifying equipment, ventilation systems, and processes to minimize the amount of a substance that gets into the workplace air. They include substitution, process control, ventilation and enclosure.
- An effective substitution example is replacing silica sand used in abrasive blasting with a safer media such as garnet.
- Wet methods as a process control will reduce dust and should be used whenever practical, particularly in cutting, grinding,
and drilling operations.
- The most effective use of ventilation as an engineering control is the removal of dust at its source. Often dust-generating tools are equipped with dust collection systems to prevent dust from spreading or becoming airborne. An essential component of these systems is the cleaning devices, such as filters, which will effectively remove dust.
- Dusty operations can be isolated by carrying them out in areas that are physically separated from non-dusty areas and keeping workers not involved in the operation out of the area. Where isolation is not effective, the process can be completely sealed off from the rest of the workplace with an enclosure.
Respirators and Protective Equipment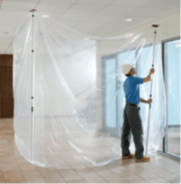
Personal protective equipment includes protective clothing and respirators. The purpose of protective clothing is to prevent the contamination of regular clothing and the transportation of silica-containing materials from the workplace. Clothing that is contaminated with silica dust should not, therefore, be worn home without cleaning.
Sometimes engineering controls and work practices cannot lower the concentration of silica to non-hazardous levels and workers must wear respirators for protection. If respirators must be used, a respirator program should be implemented. It should include written procedures for the selection, use, care, and maintenance of personal respiratory protection equipment. Workers should be instructed and trained on the care and use of personal protective equipment before using it. Some workers may have a medical condition that causes them to have difficulty breathing when wearing a respirator. Such workers should not be assigned to do work that requires a respirator if they have written medical proof of their condition.
Use, Care, and Maintenance of Respirators
The following general use, care, and maintenance procedures should be followed whenever respirators are required:
- Respirators should be used and maintained in accordance with the manufacturer’s specifications
- Proper seal of respirators should be checked prior to each use
- Storage of respirators should be in a convenient, clean, and sanitary location and stored in a manner that does not subject them to damage or distortion
- Respirators assigned for the exclusive use of one worker should be cleaned, disinfected, and inspected after each shift
- Respirators used by more than one worker should be cleaned, disinfected, and inspected after each use
- Any respirator parts that are damaged or that have deteriorated should be replaced before the respirator is used.
Ideally, respirators should be assigned for the exclusive use of one worker. But before a decision is made for a respirator to be shared by more than one worker, the following factors should be considered:
- The fit of the equipment
- The health and safety risk to the worker that would be caused by non-exclusive use of the equipment
- Any undue economic hardship to the employer that would be caused by the exclusive use of the equipment.
Respirators with a tight-fitting facepiece must be fitted to the worker in such a way that there is an effective seal between the equipment and the worker’s face. Each worker must be fit-tested for each type of respirator to be worn.
Training
Training is an important component in preventing worker exposure to silica. Control methods, measures and procedures can only be as effective as the workers carrying them out. It is therefore essential for training to cover the following:
- OSHA fit testing procedures
- The hazards of silica, including health effects and symptom recognition
- The recognition of typical operations containing silica
- Personal hygiene, respirator requirements, and work measures and procedures
- The use, care, maintenance, cleaning, and disposal of personal respiratory protective equipment.
Instruction and training should be provided by a competent person. This could be the employer or someone hired by the employer. A competent person is defined under the OHSA as a person who:
- Is qualified because of his/her knowledge, training, and experience to organize the work and its performance
- Is familiar with the provisions of this Act and the regulations that apply to the work; and
- Has knowledge of any potential health and safety hazards in the workplace.
The health and safety representative or the representative of a joint health and safety committee should be advised about when and where the training and instruction are to be carried out.
Enjoyed reading this post? Read the following articles: